Company Infrastructure
- Home
- Infrastructure
- Company Infrastructure

Infrastructure Facilities
Section | Facilities |
---|---|
Design Center | In-House Process Design - Solid Works , NX & Auto Cad |
Tool Room | In-house Tool Manufacturing Facilities |
Press Shop | Hydraulic , Pneumatic , Mechanical ; Coil Feeders |
Machining Shop | CNC Turning , Lathe M/cs. , Edge Rolling SPMs, CNC Pipe Cutting & Chamfering M/c |
Welding Shop | Robotic Arm, MIG, TIG, Spot, Projection & Rotary Welding M/cs. |
Standard Room | CMM, Contour Graph, Hardness Tester & Cupping Tester, SST Chamber Etc |
Leakage Testing | Vacuum , Forced & Dip Type M/cs. |
Captive Power Generation | 500 KVA ; 200 KVA ; 80 KVA |
Air Compressor & Air Drier | Air Comp.- 350 CFM , Air Drier - 500 CFM |
MACHINES & UTILITIES
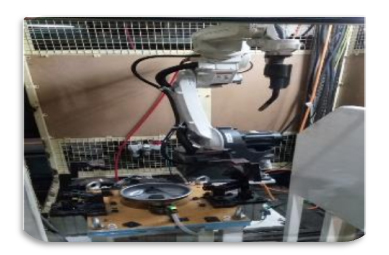
ROBOTIC WELDING INSTALLED FOR ALL TYPE OF MIG WELDING
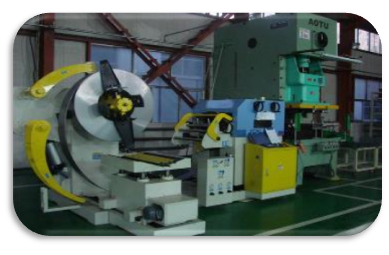
POWER PRESS WITH AUTOMATIC COIL FEEDER
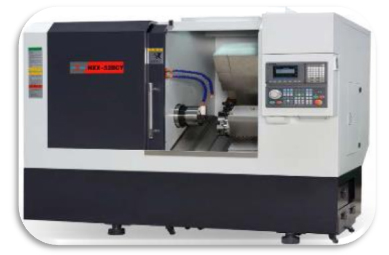
CNC TURNING CENTER FOR ALL TYPES OF TURNING COMPONENTS

EDGE ROLLING SPM TO REMOVE THE SHARP EDGE & RADIUAL PROFILE ON OVER ALL SHEET THICKNESS.
PRODUCT MANUFACTURING PRESS SHOP
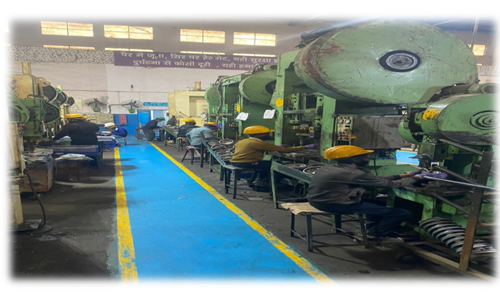
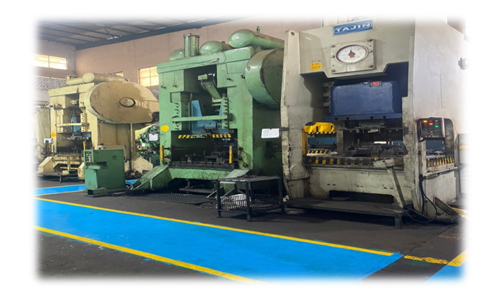
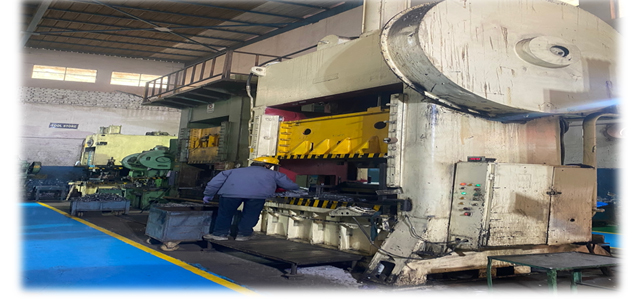
PRODUCT MANUFACTURING MACHINE SHOP
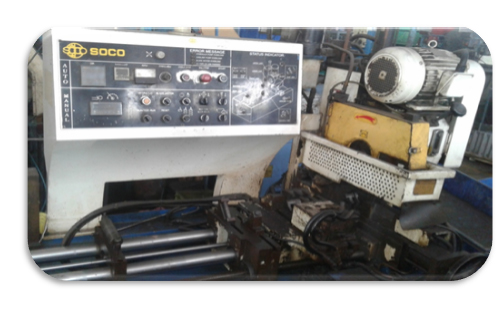
Soco M/c

Chamfering M/c
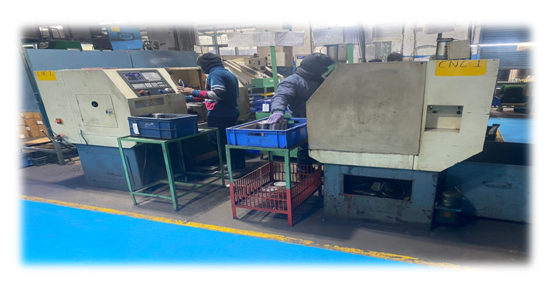
CNC Turning M/c
TOOL MANUFACTURING FACILITIES
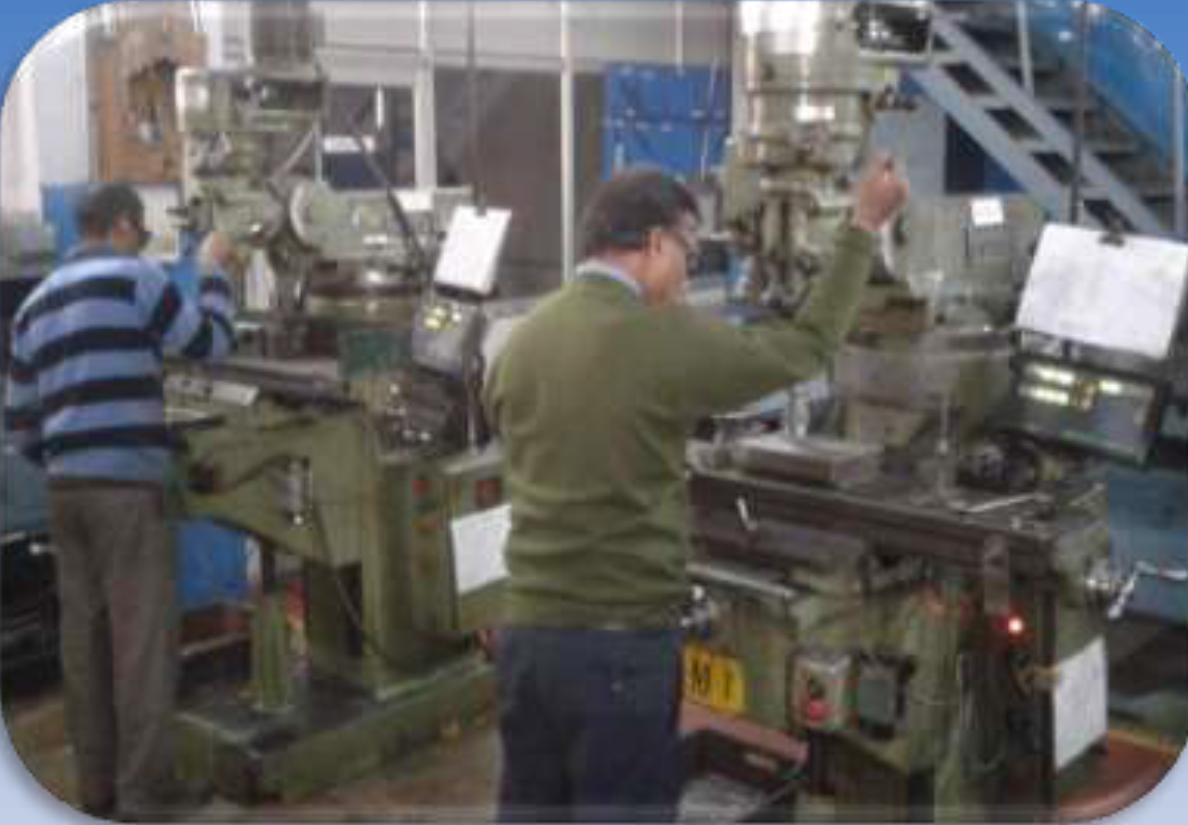
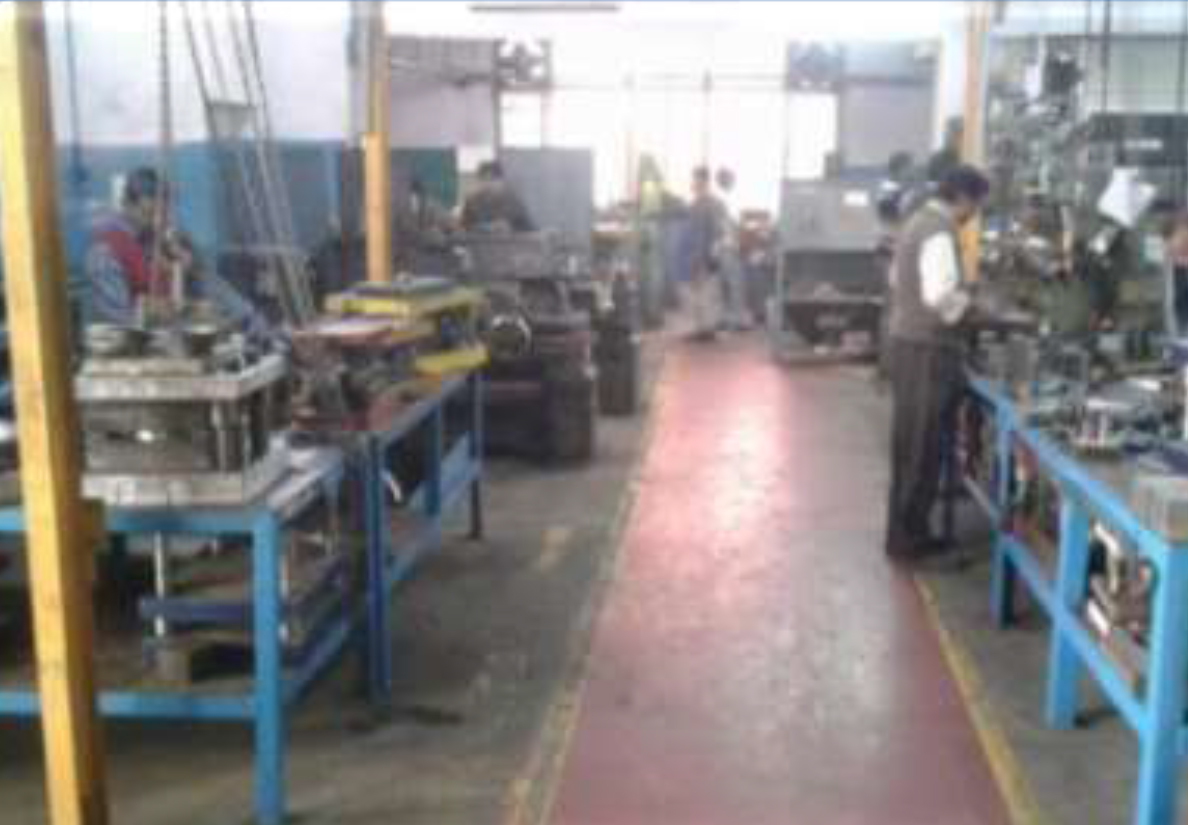
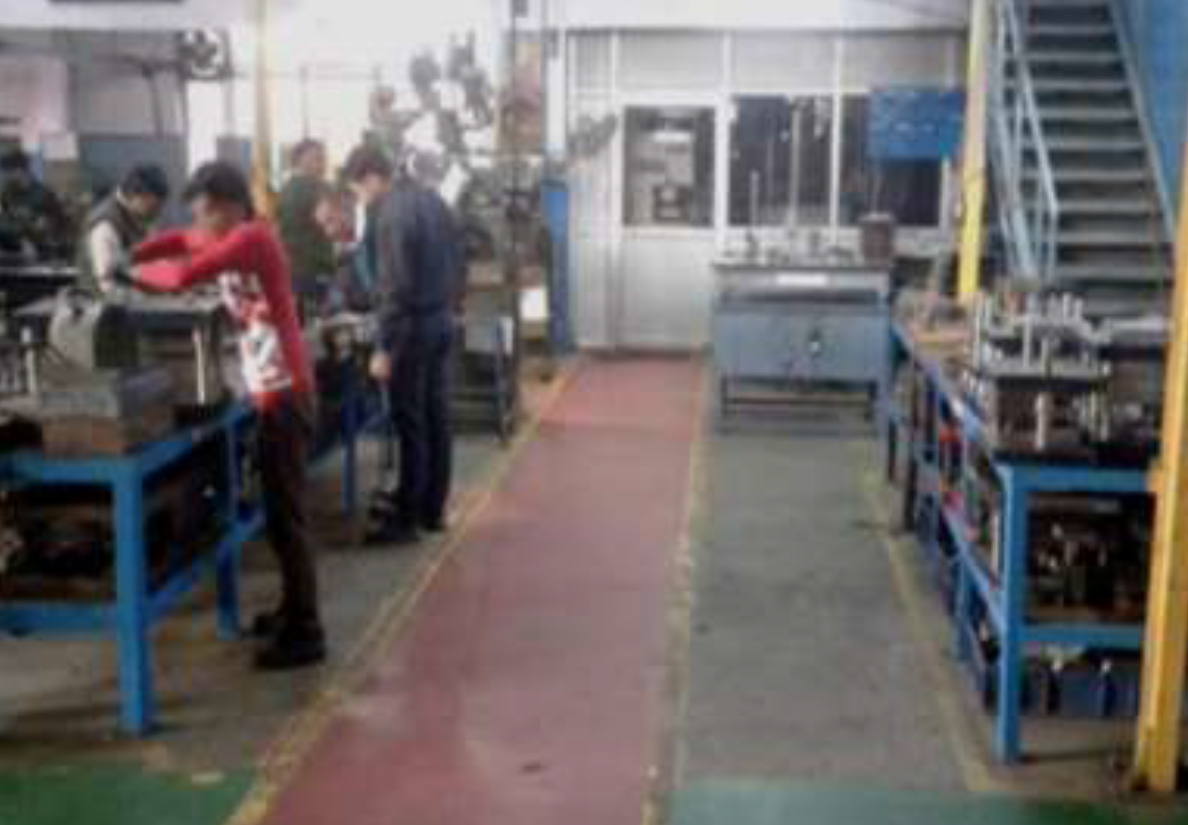
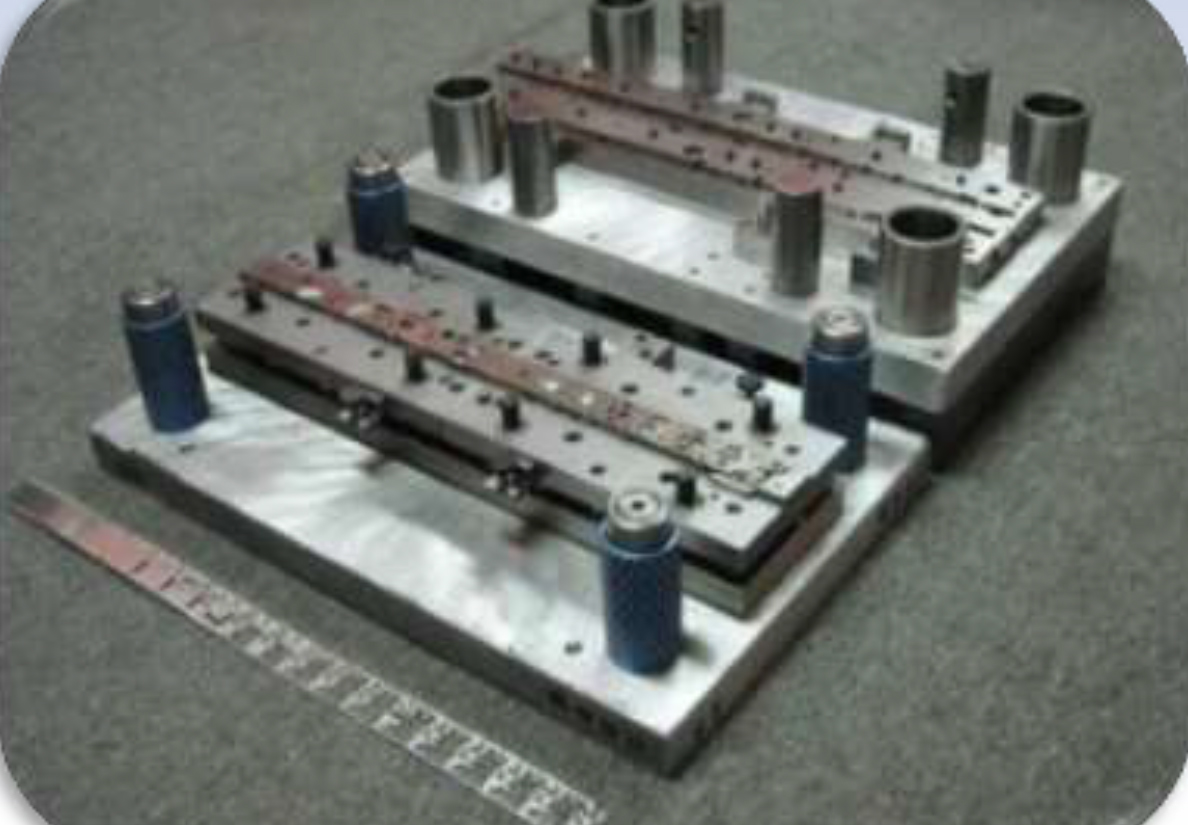
Our team is committed to providing you with insightful information on the latest trends and advancements in automobile parts. From engine components to suspension systems, we cover a wide range of topics that are shaping the future of the industry.
Our website is designed to keep you informed and up-to-date on the latest technologies and products that are being developed and tested. We strive to provide you with accurate and valuable information to help you make informed decisions when it comes to purchasing automobile parts.
TOOL MANUFACTURING
S. No. | NAME OF M/c | SPEC. | QTY. |
---|---|---|---|
1 | M1 TR | 250MM X 300MM X 500MM | 2 NOS. |
2 | LATHE | 8' | 2 NOS. |
3 | LATHE | 6' | 2 NOS. |
4 | HYDRAULIC SURFACE GRINDER | 10" X 24" | 1 NO. |
5 | SURFACE GRINDER | 8" X 18" | 3 NOS |
6 | SURFACE GRINDER | 8" X 20" | 2 NOS. |
7 | SHAPER M/c | 16" X 24" | 1 NO |
8 | RADIAL DRILL M/c | 800MM X 38 MM | 1 NO. |
9 | DRILL M/c | 1" | 1 NO. |
10 | DRILL M/c | 1/2" | 1 NO. |
11 | HYDRAULIC TROLLEY | N/A | 1 NO. |
FUTURE PLANS ( Depends on Full Capacity Utilization) | |||
S. NO. | NAME OF M/C | SPEC. | QTY. |
1 | V.M.C. | 550 X 550 X 1000 | 01 NO. |
2 | CNC WIRE CUT | N/A | 01 NO. |
3 | HYDRAULIC GRINDER | 1 METER | 01 NO. |
Machining Facilities

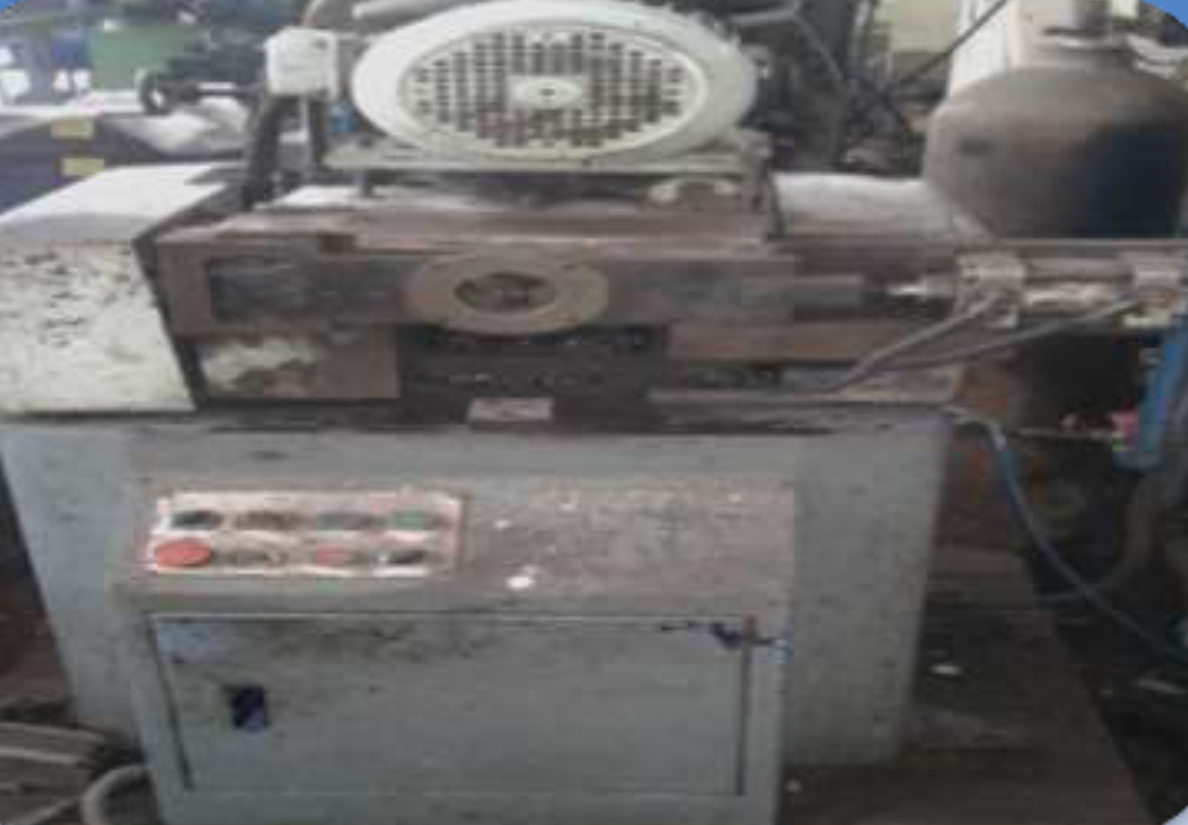
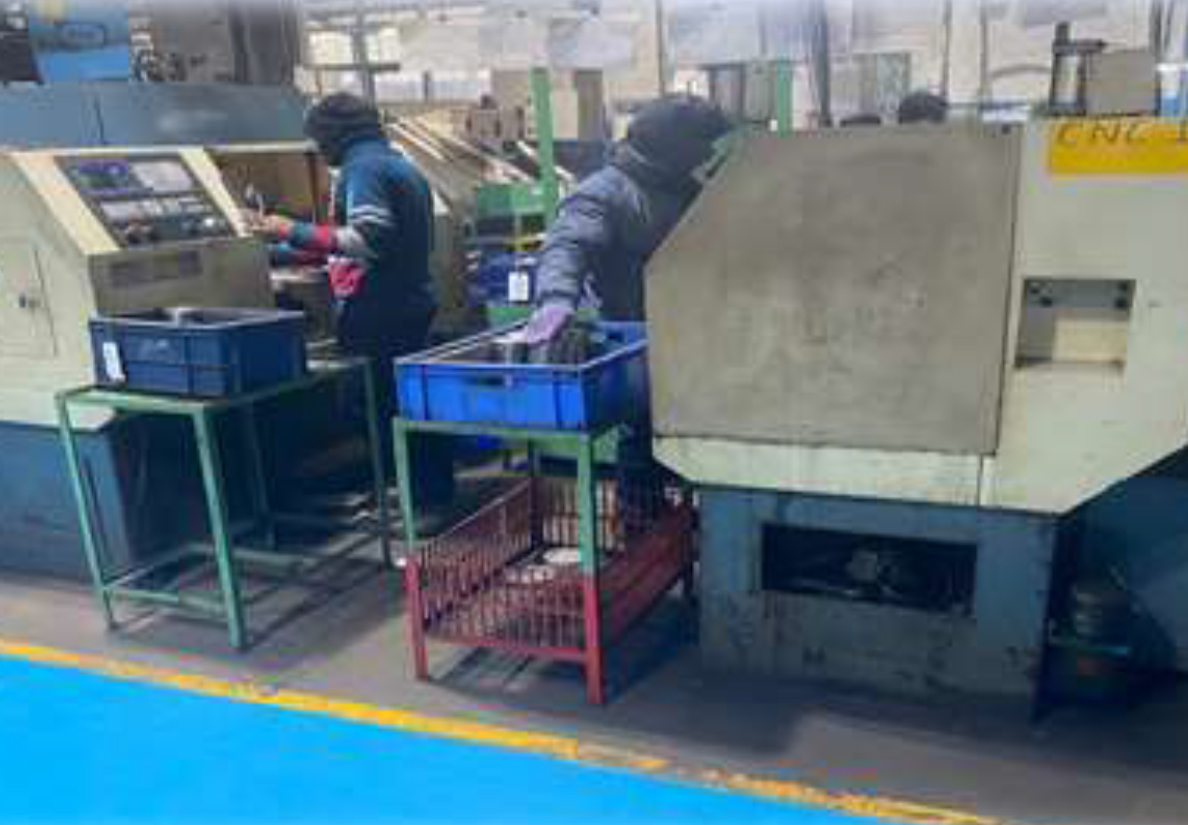
S. No. | MACHINE DESCRIPTION | SIZE | AVAILABLE QTY | SPARE CAPACITY |
---|---|---|---|---|
1 | LATHE M/C | 4 FEET | 10 | 6 |
2 | LATHE M/C | 6 FEET | 4 | 2 |
3 | CNC TURNING | 2 `` | 1 | 1 |
4 | CNC TURNING | 2 `` | 1 | 1 |
5 | DRILLING | 16 MM | 1 | 0 |
6 | DRILLING | 20 MM | 4 | 2 |
7 | TAPPING M/C | 5 MM | 2 | 1 |
8 | DRILLING | 6 MM | 2 | 1 |
9 | RIVETTING M/C | 5 MM | 1 | 1 |
10 | RIVETTING M/C | 6 MM | 1 | 1 |
Fabrication Facilities
Fabrication facilities are integral to the manufacturing process, providing a range of essential services for creating high-quality products. These facilities are equipped with advanced machinery and tools, offering services like CNC machining, laser cutting, welding, casting, and 3D printing. They enable rapid prototyping and testing of products, refining designs before production and offering economies of scale for efficient production.

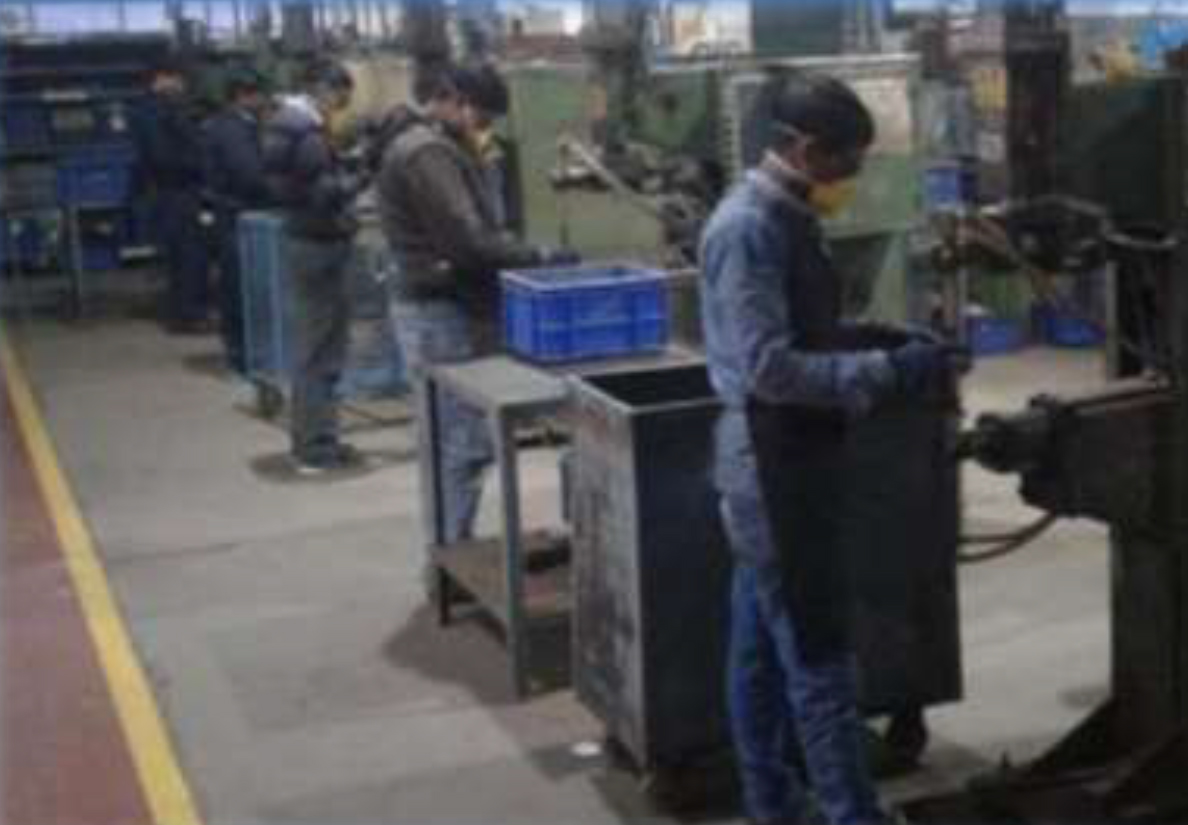
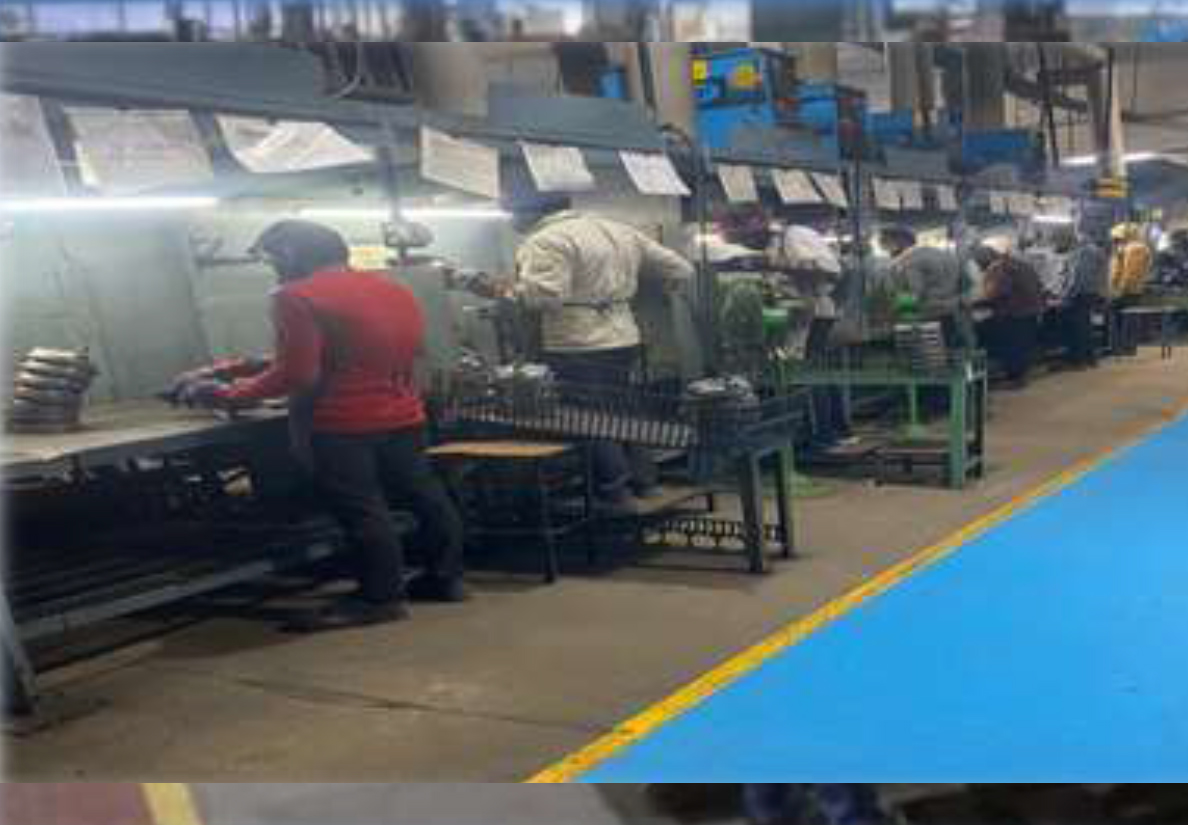
Fabrication facilities' sophistication and specialization vary, but they are critical to the modern manufacturing industry. They provide services that produce high-quality products, meeting consumers' and businesses' needs. Working with a fabrication facility can efficiently and effectively help manufacturers achieve their production goals.
S.No. | MACHINE DESCRIPTION | MACHINE CAPACITY | QTY |
---|---|---|---|
1 | MIG WELDING | 250 AMP. | 4 |
2 | MIG WELDING SPM | 250 AMP. | 9 |
3 | MIG WELDING | 400 AMP | 10 |
4 | TIG WELDING | 200 AMP. | 2 |
5 | PROJECTION WELDING | 150 KVA | 1 |
6 | SPOT WELDING | 35 KVA | 3 |
7 | SPOT WELDING | 75 KVA | 4 |
8 | ARC WELDING | 300 AMP | 1 |
Press Facilities
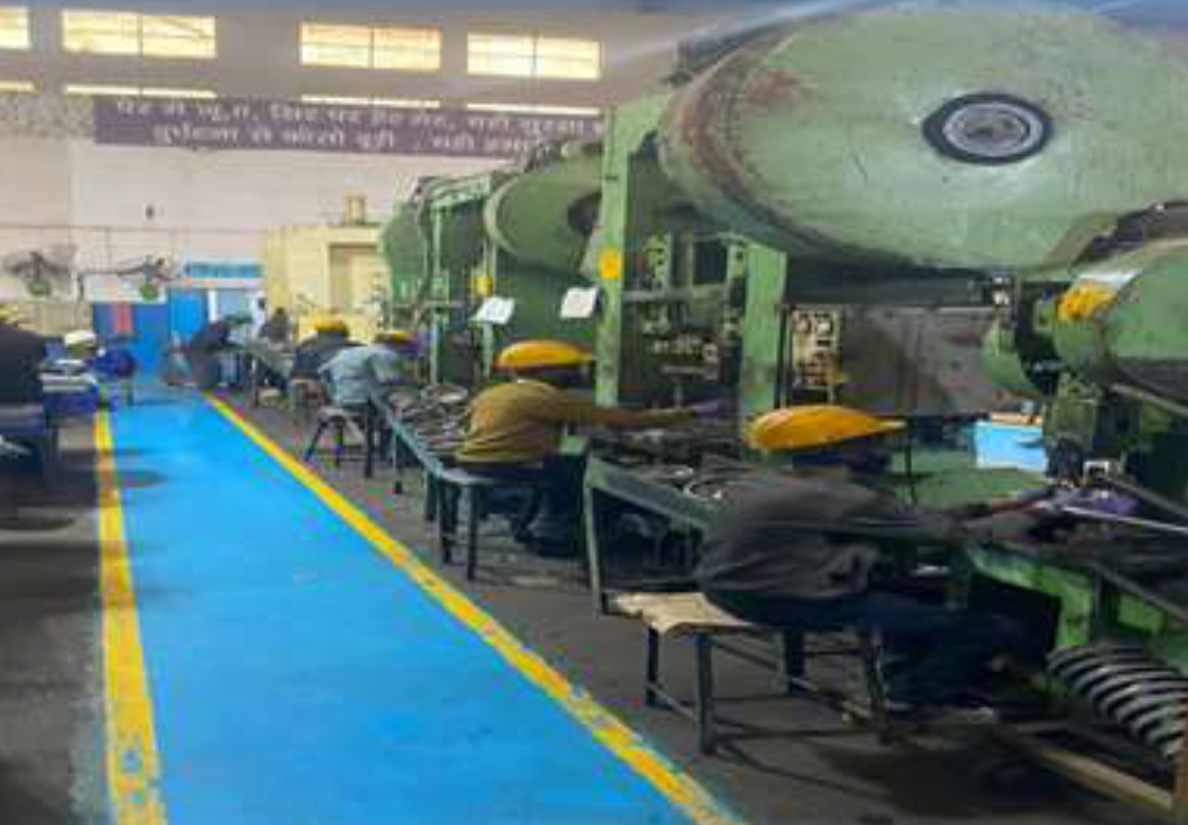

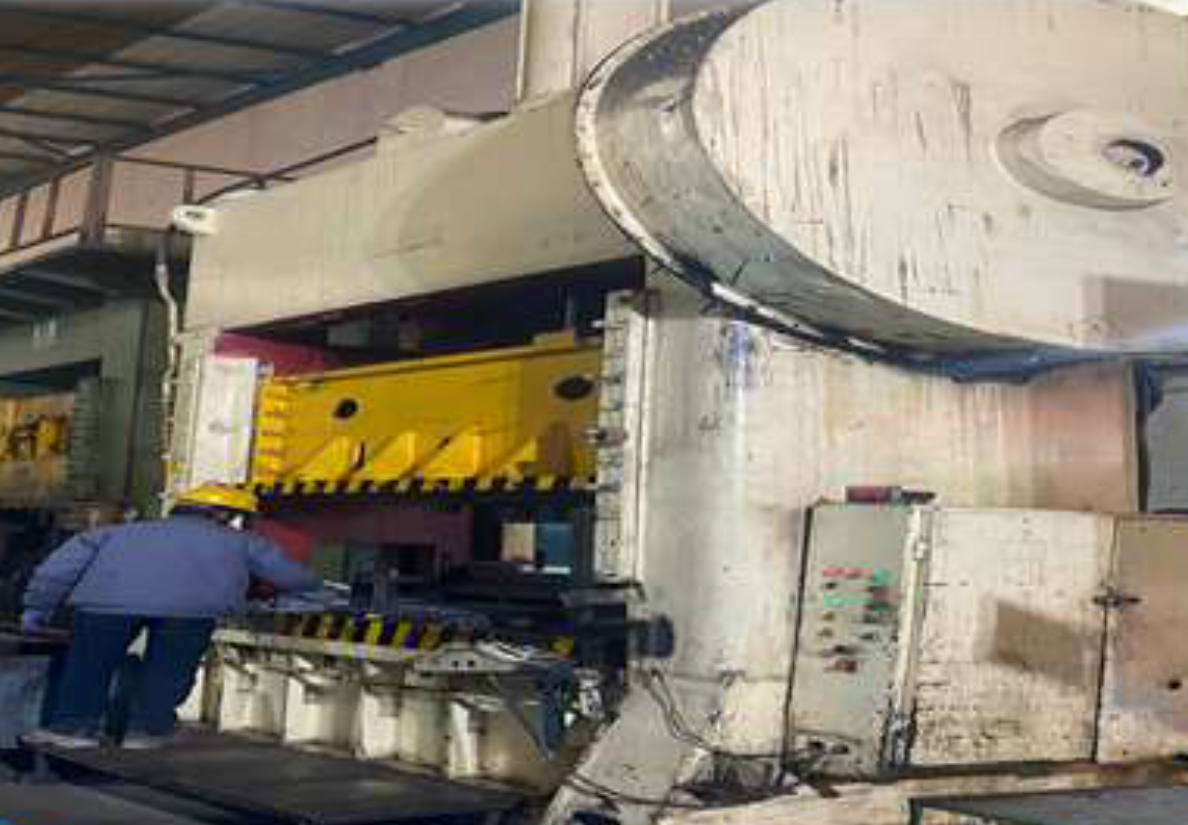
S.No. | MACHINE DESCRIPTION | MACHINE TYPE | MACHINE CAPACITY | QTY |
---|---|---|---|---|
1 | POWER PRESS | PNUEMATIC | 5 Ton | 5 |
2 | POWER PRESS | PNUEMATIC | 10 Ton | 5 |
3 | POWER PRESS | PNUEMATIC | 20 Ton | 9 |
4 | POWER PRESS | PNUEMATIC | 50 Ton | 4 |
5 | POWER PRESS | PNUEMATIC | 100 Ton | 12 |
6 | POWER PRESS | PNUEMATIC | 150 Ton | 8 |
7 | POWER PRESS | PNUEMATIC | 200 Ton | 6 |
8 | POWER PRESS | PNUEMATIC | 250 Ton | 3 |
9 | POWER PRESS | PNUEMATIC | 300 Ton | 1 |
10 | POWER PRESS | PNUEMATIC | 400 Ton | 1 |
11 | PRESS | HYDRAULIC | 100 Ton | 1 |
12 | PRESS | HYDRAULIC | 150 Ton | 1 |
13 | PRESS | HYDRAULIC | 250 Ton | 1 |
14 | PRESS | HYDRAULIC | 300 Ton | 1 |
15 | PRESS | HYDRAULIC | 400 Ton | 1 |
16 | PRESS | MECHANICAL | 75 Ton | 4 |
17 | PRESS | MECHANICAL | 100 Ton | 3 |
Our Product Range
Segment | End Customers |
---|---|
Commercial | Tata Motors |
Ashok Leyland | |
Eicher Motors | |
Daimler | |
Automotive | Maruti Suzuki India Ltd. |
HMSI - 2 Wheeler | |
HCIL - 4 Wheeler | |
Tata Motors | |
Agriculture | Escorts |
International Tractors Ltd. | |
John Deere Ltd. | |
Power | Honda Siel Power Products |
Lombardini | |
Hatz |
RAW MATERIAL GRADES & SOURCES
Raw Material Grades | Raw Material Source |
---|---|
Cold Rolled Steel | Tata Steel , Tata Bhushan Steel , Pasco ,JSW |
Hot Rolled Steel | JSW , Tata Bhushan Steel , Tata Steel |
Stainless Steel | Jindal Steel , Jindal Authorized Dealer |
Spring Steel | Stelco , Tata Authorized Dealer |
Aluminum Sheet | Hindalco, Authorized Dealer |
Copper Sheet | Vishnu Metal |
Steel Tubes | Avon Tube tech ; Ottoman Tubes ; Good luck Industry |
QUALITY CHECKING FACILITIES

Layout Inspection

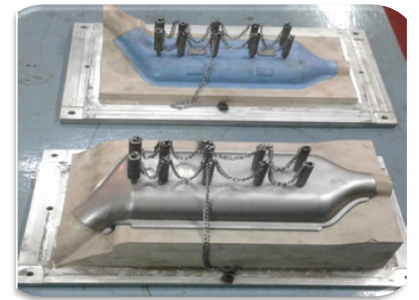
Gauges for Inspection

Contour Measurement Form tracer

Coordinate Measuring Machine (CMM)

Profile Projector
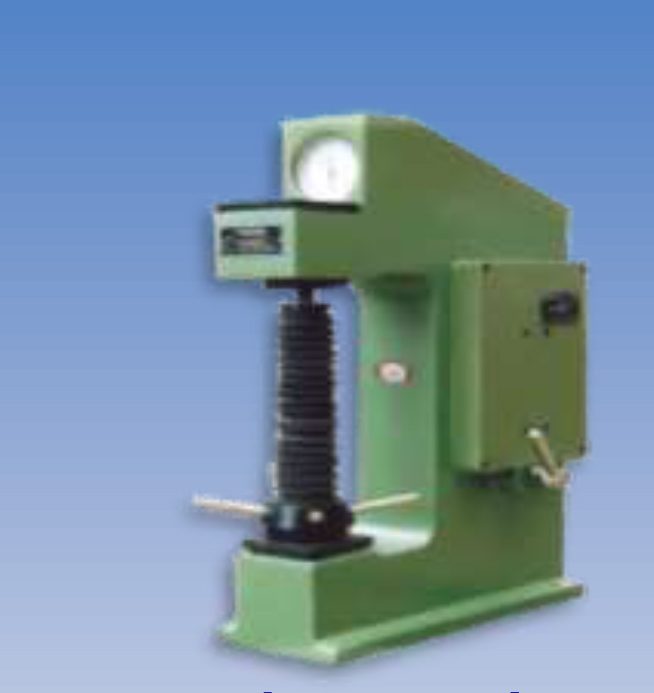
Hardness testing Machine
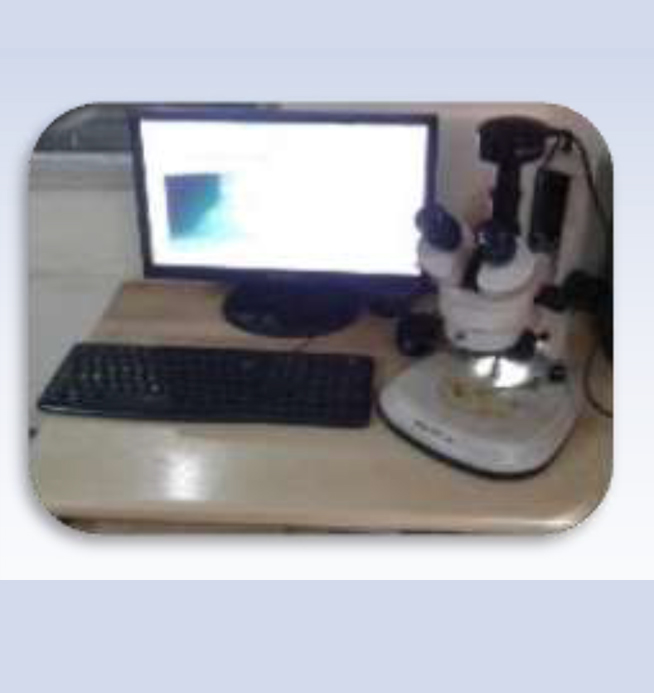
Weld Penetration Tester
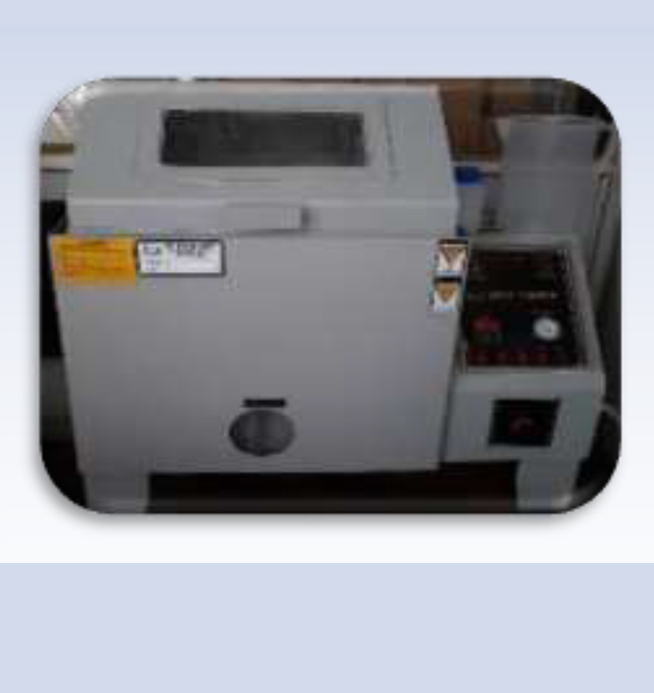
Salt Spray Test
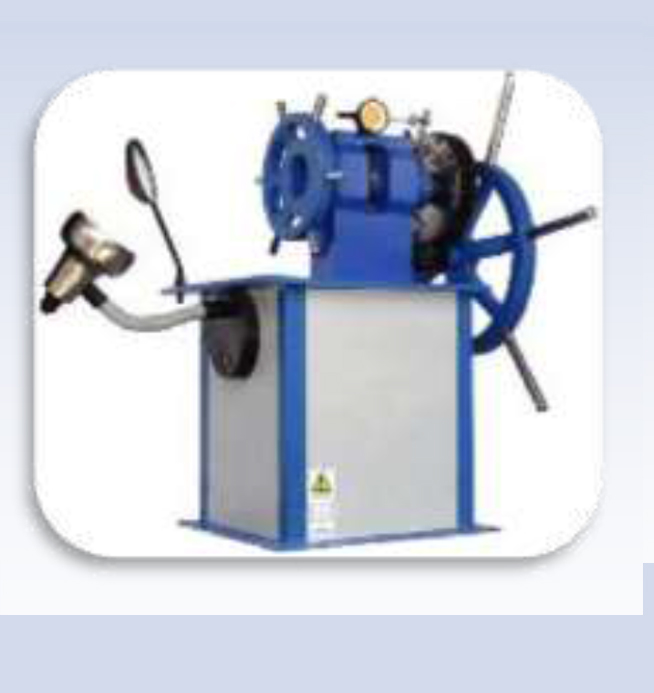
Cupping Tester
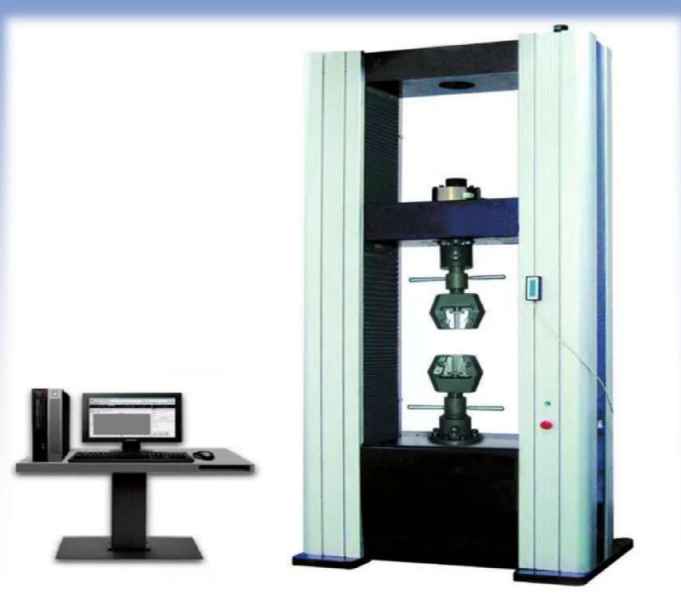
UNIVERSAL TESTING MACHINE ( UTM )
SAFETY & 5S IMPLEMENTATION

Safety Sensor Installed on Power Press

First Aid Room
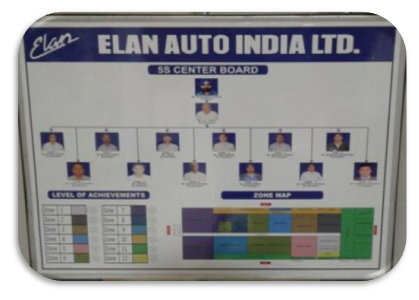
5S Center Board

Safety Instruction for PPE
Kaizen Gallery Implemented for Continuous Improvement in Quality , Safety & Productivity - Target 03 Kaizens Min / Month

DOJO ROOM IMPLEMENTED TO EDUCATE THE EMPLOYEES REGULARLY AS PER SYSTEM REQUIREMENT .


SEPARATE LOCATION DEFINED FOR DEPARMENTAL KPI`S , PLANT ACTIVITIES , CUSTOMER AWARDS , KAIZEN GALLERY & PRODUCT RANGE DISPLAY TABLE .
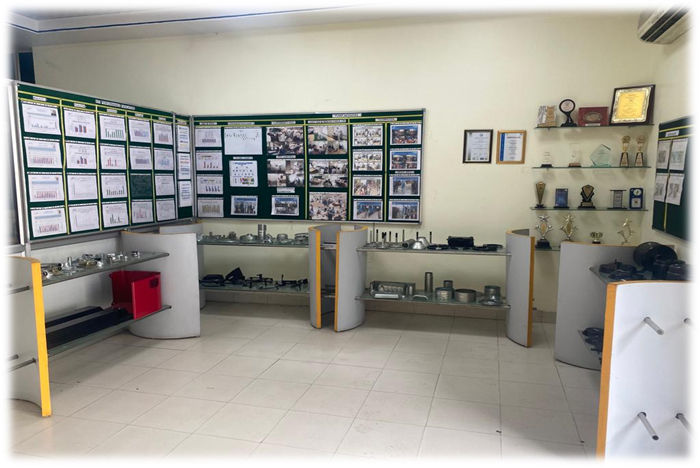
FLOOR GANG WAYS EPOXY DONE TO MAINTAIN 5S AT SHOP FLOOR AREA.
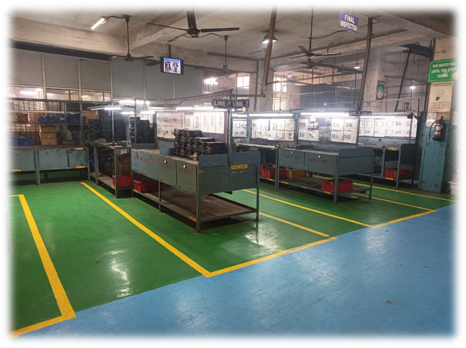
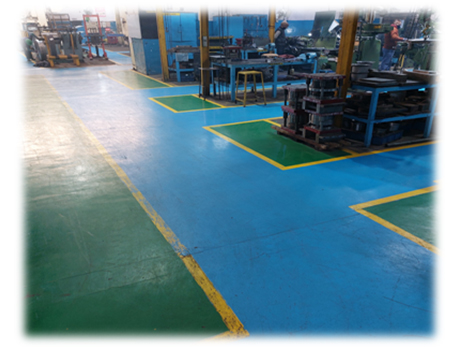
ROBOTIC WELDING INSTALLED FOR ALL TYPE OF MIG WELDING .
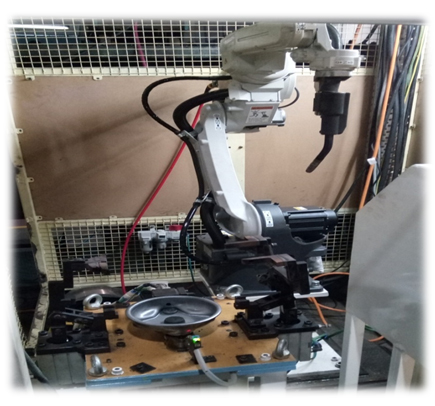
ROBOTIC WELDING INSTALLED FOR ALL TYPE OF MIG WELDING .
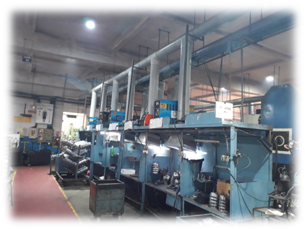
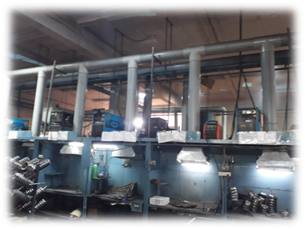
AIR DUCTING SYSYTEMS INSTALLED AT ALL WELDING STATIONS TO AVOID THE WELDING FUMES.
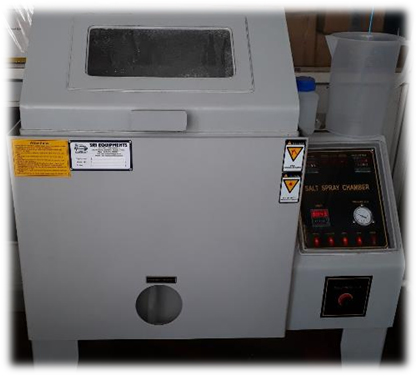
SST CHAMBER INSTALLED FOR TIMELY VERIFY SST LIFE OF ALL COATED PARTS AS PER PLAN & BASED ON THE OBSERVATION PROCESS AUDIT / IMPROVEMENTS TO BE DONE AT SUPPLIER END.
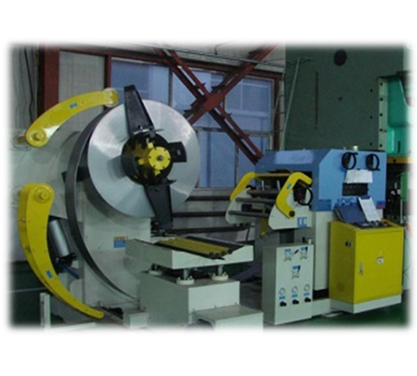
AUTOMATIC COIL FEEDER INSTALLED SO THAT RM CAN GET IN COIL FORM TO AVOID THE MISHANDLING AT SHEARING SOURCE .